Mechanical Engineering
Projects
One goal of the MSU Mechanical Engineering Program is to educate engineers who are prepared to lead, create, and innovate as their professional or graduate careers evolve. The Mechanical Engineering Design Program is the key element of the curriculum that supports this goal. There are five required design courses in the program which provide our students with eight hands-on, team-based, ‘design, test and build’ projects, and numerous opportunities to practice and refine their written, oral, poster, and video presentation skills. The Design Program in Mechanical Engineering has attracted national recognition on many occasions and helps to distinguish the ME program as one of the best in the country.
For information on becoming a project sponsor, please contact Mike Colucci.
The following were the project sponsors and projects for Spring 2017:
Slabtown Paper Shapes: Cat Scratch Saw
Our team was tasked with improving the manufacturing processes for Slabtown Paper Shapes, the Midwest’s leader in corrugated and honeycomb internal packaging. Specifically, the task was to improve the production process for cutting Cat Scratch Corrugated Build Up Blocks. The aim of the project is to develop a process allowing Slabtown to cut these blocks in a method producing less dust, increasing production time, and reducing operator risk as well as required skill.
Currently, an industrial band saw is used to accomplish the job, but the team hopes to build a design using multiple blades outfitted with variable blade spacing; this enables the machine to handle a variety of cutting jobs on the factory floor. A design that will focus on simplicity and ease-of-use will be the premier choice for Slabtown Paper Shapes. Unprocessed blocks of cardboard will need to be fed onto a belt and into the cutting area of the saw, emphasizing the least number of steps possible, thus lowering the complexity of the operation. Safety guards are installed on the machine with the health and safety of the operators and shop floor workers in mind. Increasing the overall production speed will lower the front-end production costs, enabling a higher profit margin for the business. Increasing automation of the process and lowering hands-on aspects of it can reduce worker fatigue and cut down on production time. Through innovation and integration, the MSU team strives to improve upon the manufacturing of Slabtown Paper Shapes’ product line.
Slabtown Paper Shapes: Corrugate Sheet Transfer System
Slabtown Paper Shapes is a small company located in Lansing, Michigan, that specializes in the production of corrugated industrial packaging. At the beginning of the manufacturing process, stacks of corrugated cardboard sheets are brought into the facility and run through a roll coater to create glued stacks. A two- man gluing process has been utilized for over twenty years. This process includes one operator loading cardboard into the infeed, and one operator stacking glued sheets at the outfeed. This operation accounts for 60 percent of production time, and the team’s focus is to make it more efficient through automation. If the process is reduced to one operator, it will allow multiple roll coaters to be in production at a time. This would substantially increase Slabtown’s production rate, therefore allowing them to be more competitive in the packaging industry.
The MSU team was tasked with designing a fully automated infeed and outfeed system for the gluing process. This system must be able to meet all of Slabtown’s production constraints, which includes corrugated sheets ranging in size. An automated system would allow just one operator to oversee this process. There are many solutions available in the industry today, but they require a large initial investment. Our goal is to design a cost-effective and low-maintenance solution.

Team Members (L-R): Andrew Wandor, Michael Sanchez, Brittany Galliers, Michael McAtee, Faisal Alhuwemel
U.S. Environmental Protection Agency: Test Article Tracking System
The U.S. Environmental Protection Agency (EPA) was established on December 2, 1970, to consolidate in one agency a variety of federal research, monitoring, standard setting, and enforcement activities to ensure environmental protection. Since its inception, EPA has been working for a cleaner, healthier environment for the American people.
The MSU team will focus on developing an efficient vehicle tracking system to monitor progress of test articles through the vehicle testing processes defined in NVFEL’s quality system. The project will give the EPA the ability to track the progress of test articles, starting with vehicles, in the EPA laboratory. The integration of this semi-automated tracking system with our existing processes will lend greater traceability to our laboratory quality system through each step of the testing process, and will lower overall testing costs by greatly reducing the probability of human error in the data collection process.
Meritor: Gogan Fixture Design for Brake Lining Blocks
Meritor is a tier one supplier of drivetrain, mobility, brake systems, and aftermarket solutions for commercial truck and industrial applications. Meritor is able to reach markets around the globe with locations in North America, South America, Europe, and the Asia-Pacific region. Meritor’s Brake Systems division provides dependable performance in the areas of stopping distance and reliability. Brake pad linings are crucial for slowing down and stopping a vehicle. Meritor purchases brake linings, also known as blocks, from a friction supplier. Both Meritor and their suppliers run many tests on these parts to verify they meet performance and product life expectancy requirements. One test, Gogan Hardness, measures the localized compressibility of brake linings. Meritor does not own a Gogan test machine, however, and has been performing similar compressibility tests using an Instron machine. Test results have indicated that considerable test-to-test variation exists. One contributor to the variation is the lack of repeatability for the fixture to locate and constrain the brake lining during testing.
Our team has been tasked with developing an Instron test fixture that will reduce measurement variation. The fixture design should ultimately be adaptable to both Instron and Gogan machines. Finite element analyses will be performed on each design concept to illustrate the effects of varying critical features of the fixture. The final design will allow Meritor to effectively measure the localized compressibility of brake linings.
Ford Motor Company: Chassis Dynamometer Vehicle Restraint System
Chassis dynamometer testing is an integral part of measuring fuel economy for new vehicles entering the marketplace as well as demonstrating compliance to emission requirements. In a chassis dynamometer test, the vehicle is typically restrained to the test site with wheel chocks immobilizing the non- drive wheels and straps immobilizing the rest of the car with an opposing force. The drive wheels are aligned on the dynamometer, and the dynamometer and the drive wheels rotate in opposite directions to simulate driving on a road. Although the vehicle is strapped down, changes in acceleration by the vehicle during testing can cause the vehicle to rock forward/rearward or sway laterally. On top of the movement, the current restraint system may also generate a downward force on the drive wheels that can impact the test results. Current systems require substantial time and energy from the operator to set up, and they take up valuable space in the test site. Due to these factors, the presently used restraint system is not logistically ideal and can be a source of unwanted test-to-test variability.
Ford has tasked our team with providing a CAD design for a simplified restraint system that can be easily implemented into their current two-wheel drive dynamometer test sites. The main functions for the new design are eliminating downward force on the drive wheels, reducing lateral motion of the vehicle, and creating a timely operator-friendly installation.
Tenneco, Inc.: Liquid-Gas Separator Test Bench
Tenneco, Inc. is one of the world’s leading designers, manufacturers, and distributors of clean air and ride performance products for the automotive, commercial truck, off-highway, and large engine markets and aftermarkets. As a global manufacturing company, it strives for innovative global initiatives with respect to cleaner air and smoother, quieter, and safer transportation. Headquartered in Lake Forest, Illinois, Tenneco, Inc. has 30,000 employees located in 24 countries across six continents. As a global presence, Tenneco, Inc. has various ongoing products in many different areas, one of which is a device called a liquid-gas separator.
Our team has been tasked with the specific goal of creating an innovative liquid-gas separator test bench design. A liquid-gas separator can be used to remove liquid particles from a gas flow. A device such as this normally utilizes gravity, impact force, or centrifugal force to separate the liquid from the gas. Some applications include compressor systems, oil refineries, gas pipelines, and refrigeration systems. As for Tenneco, Inc., its main use of this device is central in exhaust gas recirculation in car engines. It uses this device to filter out and redirect the liquid in the exhaust system in cars, as quickly-moving liquid droplets could collide and cause damage to blades moving at high angular velocities. The team’s design was to maximize the system’s efficiency while minimizing its size.
Ingersoll Rand – Trane: Fan Isolation and Attenuation Device
Trane is a world leader in heating, ventilation, and air conditioning (HVAC) systems. It supplies many of the world’s largest and most prestigious companies and institutions with their HVAC units. The problem that the team has been given to solve is to create a device to prevent backflow caused in the event of a fan failure in their HVAC systems, while also operating quietly. It is crucial that the system performance is not compromised in the event of single component failure. However, by adding a device such as the traditional backdraft damper, the airflow can cause the fan to produce a loud humming noise. Too much noise can be very distracting in settings such as schools or hospital operating rooms where maintaining focus is extremely important.
The team’s solution is an automatic system, such as a damper, that closes to prevent backflow if a fan should fail. The source of the noise has been identified as turbulent airflow entering the fan. A simple way to accomplish the objective of reducing noise is to redesign or optimize the current design of the damper and air inlet to smoothen the airstream. To accomplish the objectives, the group will utilize computational fluid dynamics programs such as ANSYS CFX to perform the analysis and optimize the design.
Ingersoll Rand – Trane: Casing Stiffeners of Air Handler Units
Trane, a subsidiary of Ingersoll Rand, is one of the world’s leading manufacturers of air conditioning systems. Trane produces custom air handler units at its plant based in Lexington, Kentucky. Trane produces other products, although its main manufacturing focus is air handler units. Trane’s focus is producing a cost-efficient air handler system to stay competitive in the industry. Trane’s air handler unit uses a skin of sheet metal, which is made of galvanized steel that is enclosed with three casing stiffeners and primarily held together by a foam injection. The panel assembly area is composed of five primary actions: foam injection, skin setting, spot welding, part selection and measurement, and final bending/shaping of parts.
The task assigned to our team by Trane is to develop alternative solutions for their current casing stiffener. The major criteria for the new stiffener is to ensure the air handler’s casing deflects no more than L/240 at 8” water gauge positive or negative static pressure. The ultimate goal for our team is to redesign a cost-effective casing stiffener for Trane. The L-shaped stiffeners currently being used by Trane are primarily produced by using carbon steel. Based on the detailed size of the current stiffener provided by Trane, our team is developing three main improvements: the material being used, the reshaping of the case stiffener, and the stiffener’s location on the air-handler unit.
Detroit Bikes: Bicycle Frame Preparation Machine
Detroit Bikes is the largest production manufacturer of bicycles in the US. The company cuts, shapes, welds and assembles all bicycle frames in-house at a 50,000 square foot factory on Detroit’s west side. The company was established in 2012 and supplies 24 different bicycle models to a wide range of customers. With a focus on urban markets, these high quality bicycles provide the form and function that daily riders need.
As part of the current machining process, a slot is manually cut in the seat tube using a Bridgeport mill and cumbersome fixtures. Not only does this process tie up a valuable machine, but it also causes inconsistency in the placement of the slot. The slot needs to align perfectly on the centerline of the tube for aesthetic purposes, something that does not always happen with the current tools.
Our team was asked to speed up operations of the slotting process while minimizing the use of the mill. This was to be accomplished through the design of a new machine or through modification of the current machining process. Additionally, a fixture was to be incorporated into the design that would eliminate the opportunity to misalign the slot, while keeping it perpendicular to the bottom bracket.
General Motors: Baja SAE CVT Dynamometer
Baja SAE is a collegiate design series where teams design, manufacture, and race off-road vehicles. These teams compete each year in SAE organized events across the country. Competitions are four-day long events requiring the team to balance cost, marketing, innovative design, and performance throughout a series of static and dynamic events. Previously Michigan State has used Continuously Variable Transmissions designed for snowmobiles. However, this year the team will be using a Gaged CVT, which is designed specifically for Mini Baja vehicles.
In light of this change, the Michigan State Baja team has been given the opportunity to team with General Motors in order to design and manufacture a CVT dynamometer. The dynamometer will replicate driving conditions experienced by the CVT during an event and allow for faster tuning and testing. The project will also give the team a better understanding of CVT tuning setups and allow for driveline optimization for the conditions of each event. In the future, the design team hopes that the dynamometer will be used to develop and manufacture a custom CVT.
Michigan State University Sailing Center: Portable Mechanical Sailing Dinghy Simulator
Michigan State University’s Sailing Center aids not only the university, but also the Lansing community in sailing instruction and recreation. The center has taught a multitude of people from all ages to sail using its “Learn to Sail” program. In the current teaching methodology used by the sailing center, verbal and visual explanation is available but it lacks tactile input, which makes it difficult to enable students to comprehend sailing in its entirety before entering the water. Due to the lack of tactile input, the Sailing Center has often found that students do not fully grasp the methodology of sailing, therefore causing the students’ exposure to injury.
Our team was asked to create a learn-to-sail simulator that can be placed on land to effectively teach students before being taught in the water. A sailboat will be placed on the simulator and students will be allowed on the boat to improve the efficiency, quality, and safety of sailing instruction. Ultimately, the team and sponsor believe it will not only improve instruction but also improve the safety of anyone who receives lessons at the Sailing Center.
Hitachi Automotive Systems America, Inc.: Water Pump Durability Test Stand
Hitachi Automotive Systems Americas, Inc., is a leading global Tier 1 automotive supplier of water pumps with over 40 years of water pump design, testing, and production experience. Our team is tasked to develop a water pump durability test stand for Hitachi’s Farmington Hills, Michigan location. This test stand will expand Hitachi’s testing capabilities and provide faster testing support to their customers. Water pump durability testing is needed to verify that the pump design meets durability requirements. Hitachi’s water pump durability testing is currently located in Japan. However, testing capability is needed at their Farmington Hills, Michigan location. The objective of this project is to design a water pump durability test stand capable of testing various water pump designs. The test stand requirements are:
- Belt driven via electric motor,
- Capable of testing two pumps at the same time, and
- Programmable control of RPM, system pressure, coolant temperature, and inlet and discharge restriction.
Our team has been asked to include a 3D model of the test stand design and Statement of Requirements that Hitachi can use to have the test stand manufactured.
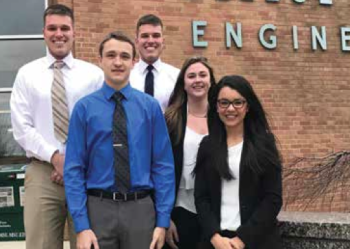
Team Members (L-R): Joshua Neubecker, Jacob Krummey, Jacob Neubecker, Taylor Mullahy, Michelle Samalik
Packsize: Variable Corrugate Box Stacker
Packsize is a packaging company that provides On-Demand Packaging (ODP) solutions for businesses with complex corrugated packaging needs. The business is headquartered in Salt Lake City, Utah and has operations in North America, Europe and Australia.
Packsize produces custom box-making technology, which allows Packsize to ship right-sized boxes in both production and distribution packaging environments. ODP replaces the traditional method of purchasing and warehousing boxes. ODP is a solution that includes an expert mix of machinery, software, accessories, consumables and services. The ODP solution reduces shipping costs and corrugated cardboard consumption by up to 40%. With Packsize On Demand Packaging®, companies receive a solution that provides them the ability to ship their products in the right sized box every time.
Our team was tasked with developing two distinctly different prototypes to support the newest Packsize product, the X4.The X4 utilizes automation to produce a box that has been cut, creased, folded, glued and labeled. The X4 reduces labor up to 66% compared to existing Packsize machines. These prototypes will provide effective and ergonomic box stacking and collection methods, which reduce labor and downtime in the box making process. The X4 is the most advanced and automated product in the current Packsize product portfolio.

Team Members (L-R): Matthew Schomisch, Martin Dwornick, Brain Wingate, Anna Sommerfeld, Joseph Rombach
Fiat Chrysler Automobiles: Effect of Drive Patterns on Transmission Design
Fiat Chrysler Automobiles (FCA), one of the largest car manufacturers in the USA, sells roughly 2 million vehicles per year. In order to keep pace with the upgrade cycle present in the auto industry, FCA US needs to create prototypes as a method of vetting designs. However, with the extremely high capital investment required for prototype vehicles, only a limited number of prototypes can be made for a given vehicle. As such, there is a growing interest in avoiding physical prototypes in favor of virtual prototypes, especially for critical subsystems like the drivetrain. Previous FCA US sponsored capstone groups at MSU have developed a MATLAB program capable of compiling real-world GPS data for vehicles into stress estimations for the drivetrain.
The goal of this semester’s project is to take these existing calculations up through the transmission to determine the time spent in each gear for a given transmission. The success of this project could have a significant impact on transmission design for future FCA US vehicles as it will enable engineers to determine how long the average consumer will spend in higher gears (7th, 8th, etc), as well as the duty cycle each gear will see.
Ford Motor Company: Dynamic Joint Friction – Driveshaft Applications
All OEM’s are actively looking for ways to reduce the noise, vibration and harshness (NVH) that occur in daily driving of vehicles. NVH contributes to continued degradation of important vehicle components due to added stresses and forces that are hard to measure due to their complexity. Ford has identified a large percentage of NVH in their vehicles, especially trucks, due to the forces in the driveshaft, specifically in the universal joint (U-joint) that connects the driveshaft to the other drivetrain components. In order to model the NVH of new designs, Ford has used computer-aided engineering (CAE) to minimize prototyping costs. To create an accurate model of forces in the driveshaft, the frictional force in the U-joint must be known. Internal frictional forces in the U-joint must be experimentally determined in order to use CAE modeling for an approximation of NVH in new designs. For this reason, a previous capstone team had built an experimental test rig. The rig consists of a drive motor, a translational slider between the motor and driveshaft, two halves of a driveshaft with a U-joint connection, and force transducers, together with other sensors that help to determine the internal joint forces. Based on the data of three previous capstone teams, a correlation has been noticed but not quantified and not yet fully proven. In order to determine a relationship between internal friction and rotational frequency, data will be captured and used to prove or disprove a relationship between U-joint friction, internal forces, and frequency, with the goal of creating an accurate CAE model.
Fiat Chrysler Automobiles: Flexible Interior Storage
Fiat Chrysler Automobiles (FCA) has tasked our team with increasing the flexibility of the existing interior storage in their vehicles, with the focus being the front cabin area. The new storage space designs need to improve upon existing features to increase functionality, versatility, and accessibility. The proposed features have been modeled to fit the next generation Dodge Charger.
The improved designs focus on revamping the cup holders and center console area. The redesigned cup holders add versatility, which allows for different sized cups to fit within the existing area. The design features a sliding mechanism, allowing them to be flipped down when they are not in use. The center console is designed for more functionality, and additional features have been added to the inside and outside of the middle console, aiming to improve its capabilities. A shelving feature will be added to the inside of the center console to allow the user to better organize their belongings while a folding tray on the outside will provide more user-friendly storage space. This tray will be stored between the center console and passenger seat and will be deployed manually. These improved features will provide the consumer with a pleasant and more efficient driving experience.
Whirlpool Corporation: Refrigerator Door Design – Storage Flexibility
The Whirlpool Corporation is a multinational manufacturer of home appliances. Its refrigeration sector is located in Benton Harbor, Michigan, and specializes in the design and development of its newest refrigerator technologies, including the 3X French Door model. This model is marketed as one of the most spacious refrigerators commercially available in the United States. Whirlpool is continuing to push the limits of refrigerator storage by expanding on the in-door storage capabilities of the 3X Model.
Our team has been tasked with the challenge of developing a new door storage system. This system is expected to have 20% more door storage space as well as a modular approach for consumer customization. All proposed solutions must be easily manufactured and cost-effective, without compromising airflow and cooling. The final designs have passed cyclic loading simulations in the Whirlpool Structures Lab and have achieved high usability rankings from Whirlpool personnel.
ArcelorMittal USA: Sampling Sleeve Disposal for Molten Steel
ArcelorMittal is a world leading steel and mining company present in 60 countries. The second largest USA facility is a fully integrated steelmaking facility located on Lake Michigan in Burns Harbor, Indiana. This plant operates two blast furnaces and is capable of producing five million tons of raw steel annually.
During the steelmaking process, different properties can be produced by chemical composition. These properties include ductility, formability and hardness. In order to ensure the correct alloying of the given steel, sampling is completed during processing. A sample sleeve connected to a telescoping probe that submerges it into the molten steel takes these samples. After the sleeve is submerged, the sample is retrieved and the empty sample sleeve is discarded.
Currently, sampling sleeves are disposed of on the ground where other recyclable materials exist; this violates environmental and recycling policies. Because these materials are not separated at time of disposal, there is an extra cost to separate recyclable materials from the non- recyclable materials.
ArcelorMittal is seeking implementation of a new process to dispose of these sleeves. This solution is both environmentally friendly and works around the current operation and layout constraints. The improved process allows disposal of sampling sleeves in a safe and effective manner.
ArcelorMittal USA: Sampling Sleeve Disposal for Molten Steel
ArcelorMittal is a world class steel producer with an annual production capacity of around 114 million tons of crude steel. ArcelorMittal is a multinational company with an industrial presence in 19 countries and a leader in all major steel markets including automotive, construction, household appliances, and packaging. During the steelmaking process, many temperature samples of the molten steel are required for analysis in order to maintain a certain set of properties for each batch. In a twenty-four hour period, over five hundred sampling sleeves are used and discarded. Currently, the disposal sleeves are thrown into a pit below large ladles transporting molten steel. In this pit, they are mixed with excess slag, inhibiting the ability to easily separate the sleeves to be recycled.
Our team was approached to develop a solution for the waste created by these sampling sleeves. A disposal system will be designed for the sampling sleeves to provide a way for them to be separated and recycled. This solution must be both environmentally and user friendly. It must be able to withstand the harsh conditions of a steel mill. An effective solution to the disposal of the sampling sleeves will greatly reduce the amount of waste created by the mill on a daily basis.
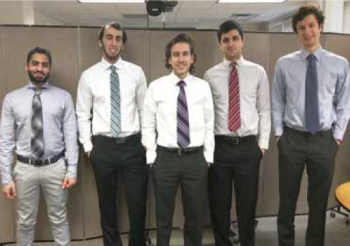
Team Members (L-R): Abdullah Hussian Alluhaidan, Jim Ryan, Alexander Starbird, Bijan Masrouri, Daniel Garberding
Peckham, Inc.: Seam Sealing Assistive Device
Peckham, Inc. is a nonprofit vocational rehabilitation organization that provides employment and upward mobility for people with disabilities. At Peckham, high performance fleece and extreme cold weather clothing are manufactured for the military, together with other clothing through commercial contracts. Within the past year Peckham has begun to use seam sealing for waterproof and lightweight garments. Seam sealing is performed with a machine that applies sealing tape to the seam of a garment by heating the tape with hot air and then pressing the tape to the seam by running it between two rollers. During the seam sealing process, two operators are generally used to properly seal longer and more complex seams on the garments.
Our team is tasked by Peckham to create an assistive device to replace the second operator for the seam sealing process. The team will develop a device that will adapt to multiple types of seams, fabrics, and tapes. This device will be easy to use for the remaining seam sealer operator and will increase the time and efficiency of the seam sealing process.
Heartwood School: Therapeutic Mechanical Pony
Hippotherapy, or therapeutic horseback riding, provides exercise that is designed to benefit those who have a physical or emotional limitation. Though not a well-defined, measureable science, testimonies of many show the impact that horse therapy can have. Heartwood School wishes to embrace this world of hippotherapy through the development of their own mechanical pony.
Heartwood School adheres to the MOVE program philosophy, which stresses the influence that physical activity can have in improving the lives of their students. In light of this, our team strived to provide Heartwood with an opportunity to engage their students in an activity that is both physically beneficial and fun. The mechanical pony acts as a three-degree-of-freedom system which introduces movements that activate core and lumbar muscles, which are crucial for stability and motor control. Maintaining the aesthetics of an actual horse provides an emotional connection that captures the students’ imagination and makes it feel as if they are going for an actual horse ride rather than performing routine exercise. The addition of a visually engaging system of riding videos and horse sounds further enhances the simulation of a real pony.
Ultimately, our team was able to implement a well- rounded design process to develop a piece of physical therapy equipment that aligns both with hippotherapy and Heartwood School’s principles. The mechanical pony demonstrates that despite the students’ limitations, they are only disabled when we deny them an opportunity.
Heartwood School: A Variety of Aids for Impaired Children
Heartwood School located in Mason, Michigan, is a part of the Ingham Intermediate School District. The school specializes in care for students with moderate to severe physical and cognitive impairments, between the ages of 3 and 26. Because of these impairments, students require continual help and support from the staff members of Heartwood. These staff members strive to enhance the ability of students to walk, and they believe each student should be given the chance to learn and succeed.
Our team was given the task of creating a guidebar for young children to be used for gait training. Another product will be created that aids staff members in the guidance of small wheelchairs and walkers so that caregivers will not have to bend or squat down to guide students. These devices, designed and created by the team, will adapt to previous methods of equipment usage at the Heartwood School. This system will allow students to learn how to make decisions on navigation, steering, and changes in direction, thereby providing increased student independence and self-confidence.
Michigan AgrAbility: Adjustable Hand Lever
Michigan AgrAbility provides critical assistance to enable people in the agricultural industry to continue working with an injury, illness or disability. Farmworkers with physical limitations to their legs have a very difficult time operating the foot pedals, which must be engaged numerous times daily, on farm machinery in order to feed livestock, work fields, clean barns and haul loads, as well as a multitude of other tasks.
In order to actuate the foot pedals safely, a considerable amount of force must be applied quickly over a relatively large range of motion. Currently, hand levers attached to the foot pedals allow workers with physical limitations to operate the agricultural machinery entirely with their hands. However, these hand levers require custom fitting for the specific farmworker because of the individual’s arm length and strength. In addition, the custom shaping of each lever for each specific tractor is required.
Michigan AgrAbility wishes to develop an adjustable- shaped lever that is modifiable in the field. Our team collaborated with a vegetable grower from Munith, Michigan, who has lost the use of his right leg due to a rare infection. A system was developed that is easily assembled and modified to significantly improve Michigan AgrAbility’s ability to help individuals with physical limitations and permit them to continue farming unhindered, thereby contributing to the public good.
Whirlpool Corporation: Under Counter Icemaker
Whirlpool Corporation, headquartered in Benton Harbor, Michigan, is a worldwide leader in the production of large home appliances. Under familiar brand names including Maytag, KitchenAid, and Jenn-Air; Whirlpool manufactures everything in the household appliance sector from refrigerators to washing machines and even cooking surfaces. Whirlpool also dominates the residential under counter icemaker market, with 15” and 18” width models that produce 40 to 50 lbs. of ice in 24 hours. These products utilize a unique method of forming ice sheets by flowing water over a cooled plate, creating ice cubes that are both visibly clear and free of sediments. However, this special process currently requires more water than traditional methods such as freezing ice in trays. Whirlpool is seeking refinements to their system that curb water usage while ensuring that the ice stays clear and mineral-free and does not clump.
Our team has been tasked with reducing the water usage of the product while maintaining the quality and quantity of ice that customers expect, and has proposed solutions that must fit within the existing structure of the appliance. Successful designs could be implemented into future iterations of the icemaker. With a more efficient product, Whirlpool can ensure that its customers are saving money and reducing their environmental impact.
Whirlpool Corporation: Under Counter Icemaker #2
Whirlpool Corporation is the leading major appliance manufacturer in the world, designing in-home solutions that help make a difference in our everyday lives. The under counter icemaker produces up to 50 lbs. of clear ice per day, free of impurities and unwanted minerals. It operates by constantly circulating water over a freezing plate. As the water freezes into ice, the minerals in the water are rejected, producing a sheet of pure, clean ice. When the sheet reaches the desired thickness, it slides onto a grid that divides the sheet into individual cubes. The water containing the discarded minerals is drained after each freezing cycle.
Our team is working to provide a method to reduce the overall water consumption in the existing product. A prototype design will be compatible with the current general structure of the existing icemakers and will maintain the production of high-quality ice.
MSU Adaptive Sports and Recreation Club: Hand-Cycle Propulsion Adapter
The MSU Adaptive Sports and Recreation Club has a current hand-cycle, the Pacific Handy Upright Hand-Cycle that, while useful to many of their athletes, is unable to provide a cycling experience to club members with more limited ranges of motion. The propulsion system on the hand-cycle is an in-phase dual crank, which requires the users to extend their arms to move the handlebars in a circle in order to rotate the gears. This motion, combined with an inability to adjust the seat position closer or further from the handlebars, results in a hand-cycle that is exclusive to those who have strong control over their torso and adequate upper body strength.
In order to provide a permanent solution for the Adaptive Sports and Recreation Club, our team has decided that the best course of action is to provide the club with an entirely new hand-cycle that will facilitate a cycling experience for athletes with limited ranges of motion. Input from Industrial Advisors (Piotr Pasik and Stephen Blosser) will be considered to ensure that the following criteria are met: the hand-cycle is designed with regard to the athletes that will be using it, and that it will be a long-lasting solution for the club.
Bosch: Welding Fixture for Turbo Wastegate Lever
Bosch Mahle Turbo Systems (BMTS) develops and produces tailor-made, exhaust-gas turbochargers for passenger cars and commercial vehicles. With the current demand for more efficient and higher powered engines, turbocharger systems have become more popular on a wide range of vehicles. Turbocharging can increase the power and efficiency of an engine without increasing the size. Wastegates are a critical sub-system of turbochargers. They release the backpressure of the exhaust gasses when reducing engine load.
Currently BMTS North America relies on BMTS Headquarters in Germany for turbo-system prototyping. Without support from Germany, North American sample parts often get pushed back or not finished in a timely matter. A solution to this is to make the sample shop located in Farmington Hills, Michigan more capable of producing prototypes.
Our team is tasked to design a fixture and welding apparatus to complete the turbo assembly process. This would allow setting and welding of the wastegate actuator lever to the wastegate spindle. The fixture and welding apparatus will accommodate two turbo assemblies, one with a pneumatically actuated wastegate and one with an electronically actuated wastegate. A successful design will have a low processing time and accuracy of desired specifications which include actuator set specs, weld quality specs, and lever position specs. The completed project will save time and money for the BMTS North American branch, while reducing workload for the BMTS Headquarters in Germany.
Fiat Chrysler Automobiles: Composite Low Cost/Low Weight Jack
Fiat Chrysler Automobiles (FCA) is the world’s seventh largest automaker. FCA brands are Chrysler, Dodge, Jeep, Ram, FIAT, Alfa Romeo, Maserati, Lancia, and Abarth. As with all automakers, FCA must meet impending emission standards around the world, including the United States’ Corporate Average Fuel Economy standards. One way to meet these is to reduce the weight of the car, however the cost of a component ideally should not increase as its weight decreases. Recent technological advancements allow incorporation of composite materials in place of metals in automobiles. Use of composites can decrease the weight of components and allows for alternative manufacturing methods.
FCA has requested the redesign of the metal scissor jack included in its vehicles. The result of the redesign is a lower weight, affordable jack capable of production in volumes of up to one million units annually. The redesigned jack incorporates composites for major structural components in place of steel. The price of the jack was minimized throughout the design by optimizing the amount and type of material used. The composite jack meets the same testing requirements and has or will complete the same tests as the steel jack. All packaging constraints are met, including fitting within the spare tire compartment of the Chrysler 200.