Mechanical Engineering
Projects
One goal of the MSU Mechanical Engineering Program is to educate engineers who are prepared to lead, create, and innovate as their professional or graduate careers evolve. The Mechanical Engineering Design Program is the key element of the curriculum that supports this goal. There are five required design courses in the program which provide our students with eight hands-on, team-based, ‘design, test and build’ projects, and numerous opportunities to practice and refine their written, oral, poster, and video presentation skills. The Design Program in Mechanical Engineering has attracted national recognition on many occasions and helps to distinguish the ME program as one of the best in the country.
For information on becoming a project sponsor, please contact Mike Colucci.
The following were the project sponsors and projects for Fall 2016:
MSU Adaptive Sports & Recreation Club: Athletic Walker
The MSU Adaptive Sports & Recreation Club is an organization that provides a welcoming environment and exercise resources to people with physical disabilities. The goal of this project is to create a safe, durable, and ergonomic posterior posture walker that easily moves with the user during a sports application. This device is intended to be used by persons with partial control over their lower limbs. The adaptive walker can be used on a variety of surfaces such as a track, turf, and a basketball court. The intent is to allow users to utilize their full body when exercising, rather than being constrained to a wheelchair. The team worked closely with members of the adaptive sports team to gather input and target key issues with current walkers. The main focuses of the new design were ergonomic handgrips, a foot shield for the back wheels, and a quick switch to lock/unlock the front wheels. These unique concepts combined to allow a safe but adaptive environment.
Steelcase: Overhead Conveyor Hang Fixture Stabilization
Steelcase is the world’s largest manufacturer in office, health, and education furniture. The company’s products and services create spaces that amplify the performance of people, unlocking their human promise. For more than 100 years, Steelcase has worked with leading organizations to provide great experiences for their people.
Currently, Steelcase is seeking to convert its powder paint shops to robotic painting in order to achieve improvements in quality and powder transfer efficiency and to meet increasing skill requirements.
The main factor that hinders a conversion stems from the robot’s inability to effectively paint due to swaying of the products moving through the booth. This swaying is caused by vibrations in the system that can lead a part to make contact with the nozzle of the paint gun as well as result in accuracy errors when painting.
For this project, the group delved into solutions that helped stabilize the swaying motions in the parts to their required tolerance. The idea of an eddy current damping station in order to stabilize the parts was proposed, and the team was asked to begin the steps into development of the design. Plans towards development were addressed to prove conceptually which ideas could be produced. Accomplishing this required modeling of the system mathematically, determining which items were necessary to be purchased, optimizing the placement of these items, and lastly demonstrating this system with a scaled-down model to prove the dampening effects.
General Motors: Directional Speakers and/or Systems
General Motors has a growing line of electric and electric-hybrid vehicles. Electric vehicles are nearly silent when in operation because of the lack of an internal combustion engine. While this is a selling point to the drivers of the vehicles because they prefer a silent cab, it can cause an issue to people outside of the car. If the vehicle is nearly silent, it can be dangerous to pedestrians because they might not be aware of the presence of the car.
The objective of this project was simple: develop a noise generation system to project noise outward from the car at a specified frequency and decibel level in order to make aware the presence of the car to the environment. Simultaneously, the noise created by our system must also be cancelled in the cabin of the vehicle so that the driver experiences a nearly silent ride.
Hitachi Automotive Systems Americas, Inc.: QFN Solder Joint Robustness
Hitachi Automotive Systems Americas, Inc. manufactures and markets a broad range of electromechanical and electronic automotive products for all major automotive original equipment manufacturers. Based in Farmington Hills, Michigan, Hitachi has historically been synonymous with safety, quality, growth, and continuous improvement.
As vehicles become increasingly computer based, automotive companies are asking for smaller circuit boards that have greater capabilities and remain robust to harsh vehicle environments. As a response to these requests, Hitachi Automotive Systems and other electronics suppliers are switching their electronic components to Quad Flat No-lead (QFN) devices in order to save space. These QFN components are soldered to the circuit board but have smaller leads than the standard leaded devices. The smaller leads on the QFN devices are cracking when the heat sinks, which are under the circuit boards, deflect vertically during thermal loading.
Our team created, organized, and carried out a test to determine which heat sink cross-sectional area will allow for the most vertical deflection of the heat sink before QFN failure. The design team ran finite element analysis alongside mechanical testing to simulate the thermal load, quantifying the stress distribution. The internal stress values of the board at the location of the failure can be used to predict failure in other Hitachi PCBs and in future electronic controller design.
Packsize: Corrugate Laser Cutting and Creasing
Packsize is the world leader in on-demand packaging, providing customers with the ability to create the right sized, custom box on the fly. This is accomplished by utilizing machines designed and manufactured by Packsize. These machines cut and crease corrugated cardboard into the right size and configuration for the customer’s specific needs. With this technology, their customers reduce shipping costs, use less corrugated material, minimize void fill (air pillows, packing peanuts, etc.), reduce or eliminate premade box inventory, optimize warehouse space, reduce labor, and increase environmental sustainability. Packsize wishes to increase their machine capabilities even further through the use of laser technology.
Our design team was tasked with looking at laser effectiveness in relation to corrugated material. This project required the team to research different types of lasers and their capabilities. The design process began with understanding the different laser parameters to design better tests for identifying the laser’s ability to cleanly and effectively cut and crease corrugate. Packsize helped the group obtain a laser and corrugate samples for testing. The group used process design to develop tests that analyze the significance of laser power, speed of cutting, and other parameters. The group executed its tests, analyzed the results and optimized the laser settings. This was done through an iterative process to best identify the effectiveness of cutting and creasing corrugate. Throughout this project, the team focused on safety as a critical design and testing factor.
Ingersoll Rand – Trane: Custom Air Handling Unit Panel
Trane, a brand of Ingersoll Rand, produces high- quality air handling units (AHU) for industries such as health care, education, government, etc. They have been offering custom AHUs with high performance in air leakage and casing deflection for over 20 years; however, they would ideally offer more flexibility to customers seeking a cost-effective option. Because of this, Trane is losing to competitors such as Leibert, Silent-Aire, Energy Labs, and Haakon, who offer flexibility by producing AHUs for customers seeking less robust designs compared to Trane’s.
Our design group benchmarked the AHU industry to determine the best approach to designing an alternative cost competitive panel for Trane while keeping a class-A certification. Working closely with Trane’s product engineering, marketing, and customer service, they further developed the design and determined the desired target cost for the new panel.
Utilizing finite element analysis (FEA) software, ANSYS, we analyzed cost-cutting designs based on load and certification requirements provided to us by Trane. Our design group produced two final design alternatives in Siemens NX and presented them, along with FEA studies, to Trane for its consideration. With a cost competitive alternative to its custom AHU, Trane will spearhead the market and once again become the leading custom AHU manufacturer in the industry.
Ingersoll Rand – Trane: Externally Mounted Impeller Exhaust Hood
Trane Inc. is a subsidiary of Ingersoll Rand Inc. located in La Crosse, Wisconsin. It is a world leader in air conditioning systems, services, and solutions. Trane offers a wide range of energy- efficient systems including heating, ventilation, and air-conditioning. Trane’s CSAA product line features various sizes of industrial air handlers designed to clean, filter, dehumidify, heat, and cool commercial buildings with superior performance, industry- leading efficiency, and tailored specifications to satisfy the unique demands of each customer.
Trane has been utilizing motorized impeller fans for multiple applications in its CSAA line, and these fans can be used for its return air systems as well as its supply air systems.
In the current design, the impeller fan is mounted internally, which increases the overall size of the unit. Our team’s objective was to create a reduced overall length exhaust fan design for the two different size options of CSAA air handlers. The motorized impeller exhaust fans were externally mounted to a foam-injected two-inch parallel panel. The project includes two alternative designs for the fans depending on the unit. An exhaust hood was be designed to cover the fan and was tested by our team.
Tenneco, Inc.: Characterization of Phase Change Materials
Tenneco, Inc. is a global company leading in the designing, manufacturing, and distribution of automotive clean air and ride performance products. Tenneco’s vision is to pioneer global ideas for cleaner air and smoother, quieter, and safer transportation. A breakdown of the company’s clean air business includes reduction and control of criteria pollutants, greenhouse gases, and acoustic noise.
With the increasing need to make automobiles more efficient, losses of energy through heat have the possibility to be recovered and used in different areas of a vehicle. Our design team worked on the research and testing of Phase Change Materials (PCM) in a Hybrid Electric Vehicle (HEV) battery cooling system. PCMs are substances with high latent heat capacities which allow for absorption and storage of energy at a constant temperature. These materials can hold more thermal energy between phase changes, which make them great materials to capture energy and transfer it for use in other areas of an automobile.
We identified PCM materials that can be used to capture heat emitted from a HEV battery system, a means to ensure proper energy transfer to and from the PCM, as well as efficient transfer of the PCM stored thermal energy to various chosen applications in the vehicle.
Bosch: Test Fixture BLDT Diesel Pumps
The Bosch Group is a leading global supplier of technology and services. The company employs approximately 375,000 associates worldwide (as of Dec. 31, 2015) and generated sales of $78.3 billion in 2015. Its operations are divided into four business sectors: Mobility Solutions, Industrial Technology, Consumer Goods, and Energy and Building Technology. The Bosch Group comprises Robert Bosch GmbH and its roughly 440 subsidiaries and regional companies in some 60 countries. If its sales and service partners are included, then Bosch is represented in roughly 150 countries.
The Diesel Systems group at Bosch supplies high pressure cylinder pumps to their customers as part of the common rail fuel system. As part of the release testing a bearing load drive torque (BLDT) measurement must be completed. This requires stain gauges to be installed on the driveshaft of the pump. Once the pumps are instrumented, it is imperative pumps be tested on a fuel system bench prior to being installed on a test engine. This is especially true on BLDT pumps as the strain gauges are extremely sensitive and prone to failure.
The project being completed by the MSU Capstone team will increase the efficiency of testing BLDT instrumented pumps by reducing test bench down time and reducing the risk of fuel contamination. It will also provide a higher quality of testing as some instrumented pumps that cannot currently be tested on our benches, will now be able to be tested insuring the pumps are properly instrumented prior to being installed on an engine.
Hitachi Automotive Systems Americas, Inc.: BNA Lash Study
Belt-Drive Electric Power Steering (BEPS) is replacing the older hydraulic steering pumps. BEPS offers many advantages; BEPS is lighter than the hydraulic steering system and it does not require power from the engine. This leads to an overall increase in the vehicle’s performance and fuel economy. Additionally, BEPS provides more freedom in defining the performance characteristics to better match the target vehicle. For example, the same gear could be used in a truck and a sports car.
As shown in the diagram, the rack has a groove, or thread, in which sit the ball bearings located inside the ball nut assembly (BNA). The ball bearings do not fit perfectly within the grooves where lash greater than 30 microns is undesirable. If there is no lash, there will be increased friction; while a lash too high will facilitate noise conditions.
The goal of the project was to directly measure the lash between the BNA and the rack. In order to do so, the team needed to prevent the BNA from rotating while moving the rack back and forth. The movement of the BNA was measured via a laser or force cell measurement system.
Meritor: Optimized Axle Carrier Structure
Meritor is a global leader in advanced drivetrain, mobility, braking, and aftermarket solutions for the global commercial vehicle and industrial markets. With the goal of meeting the customers’ needs, Meritor strives to develop innovative products that provide superior performance, energy efficiency, and reliability.
In an effort to reduce the cost and weight of the carrier structure on the rear drive axle of trucks, Meritor is looking to implement a thrust bearing to counteract the gear forces directly, where the loads are applied by the pinion gear onto the ring gear. During overload conditions, the pinion gear faces some deflection, which is inefficiently absorbed by the carrier structure. With a thrust bearing implemented, the load will be directed to the carrier structure directly through this device. The point that this force enters the carrier structure is known, therefore allowing the carrier structure to be optimized to absorb the desired amount of force with the least amount of material. This result decreased the weight of the carrier structure, decreasing costs and increasing fuel efficiency. The improved carrier structure and thrust bearing also decreased the deflection of the pinion gear, decreasing the wear on the pinion and ring gears and increasing lifespan and performance.
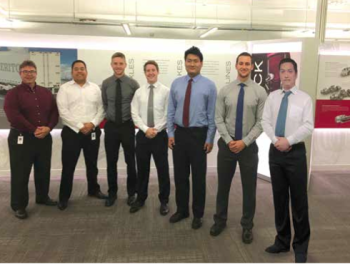
Team Members (L-R): Ed Gebal, Pedro Garcia, Andrew Kalina, David Meleca, Luyhi Chen, Dan Blair, Yuzhuo Gu
Ford Motor Company: Driveline Joint Friction
Ford Motor Company is one of the largest automotive manufacturers in the world with large markets in Europe, Asia, and North and South America. Headquartered in Dearborn, Michigan, Ford produces some of the most dependable and long-lasting vehicles. To ensure that the company remains competitive in the increasingly competitive auto industry, Ford engineers are designing their products with the “Go Further” mentality. To improve the driving experience, Ford’s Powertrain NVH Research and Development department partnered with Michigan State’s engineering department. Ford is currently unsatisfied with their ability to model friction in their Computer Aided Engineering models and is working with Michigan State University to develop a device capable of identifying the dynamic friction losses in their driveshaft joints. Ford can use the results from this project to significantly reduce development times and costs in the future.
The test fixture that Ford requested will be able to accurately measure articulation torque vs the angle of the joint in real time and produce hysteresis plots. The fixture will be able to apply various articulation speeds and torques on the shaft while filtering out possible noise in the data due to the mechanical properties of the system.
Marathon Petroleum Corporation: “Pig” Transmitter Functionality
Pig tracking devices have been found to fail during nitrogen purges of pipelines. Several failure modes were hypothesized. The design team investigated the effects of temperature and force on Pig Transmitter functionality through the use of experimental methods. These failure modes were examined because they were identified as the most probable causes of failure.
To determine the effects of temperature on the tracking devices, the conditions of the pipeline were simulated. A transmitter was placed into an insulated chamber and cooled. Throughout the experiment the amplitude of the transmitter signal was measured against the temperature of both the air in the chamber and the surface temperature of the device. The data was then analyzed to determine the temperature at which the transmitter failed.
The forces present on the tracking device during operation were reproduced to determine the effects of force on transmitter functionality. An impact test was performed directly on the transmitter. The force applied to the transmitter was increased with each trial of the experiment. During testing, the amplitude of the device signal was again monitored to determine the force at which failure occurred.
By receiving and interpreting results from these tests, Marathon can determine why their Pig Transmitters are failing and implement a design to correct the issue, making their Pigs more reliable

Team Members (L-R): Craig Miller, Jeremy Reisig, Matthew Gagnon, Herbert Darrow, Eric Olsen, Alexander Ho, Brett Hewitt
Michigan AgrAbility: Tractor Step Bracket
Michigan AgrAbility provides services to farmers with disabilities, illnesses or aging conditions. It develops farming tools, equipment, and methods to allow farmers with disabilities to continue their productive work and lifestyle.
Farmers with physical limitations to their legs have a very difficult time climbing the first step of tractor ladders. The first step to a tractor is especially high off the ground, usually 22 inches. This large distance causes strain on these farmers. In order to account for this, commercially available folding bed steps can be used to eliminate this large distance. The goal of this project was to fabricate a bracket that secures the bed step to the bottom step of a tractor ladder. This allows for farmers to easily climb on the tractor as well as resolve the need of the first step being high from the ground.
Tenneco, Inc: Liquid Gas Separator
The problem to be solved for Tenneco, Inc. was to create a new concept idea and prototype for a liquid gas separator (LGS). A benchtop testing rig was also to be created to test the efficiency of the LGS.
Applications for an LGS include exhaust gas recirculation condensers, HVAC, refrigeration, A/C, and kitchen ventilation systems. In all applications, it is useful and necessary to separate the contaminants from the inlet airflow.
Our focus for the LGS was the EGR application. While considering the high pressures and temperatures of an EGR and other constraints, we operated our LGS prototype at room temperature and lower pressures.
Our solution process included a literature review of LGS methods in the market, brainstorming, choosing best design, analyzing the design using models/ calculations, optimizing, and building a desktop demonstrator. For the desktop demonstrator, there needs to be a method of supplying the saturated air/ vapor mixture into the inlet of the LGS. A pressure of around 1 bar was required.
An optimal LGS will have both a low pressure drop and high efficiency (rids air of moisture). The goal for this project was to create innovative methods for separating liquid from an air/vapor mixture and creating an efficient way of testing and qualifying the LGS.
Environmental Protection Agency (EPA): PEMS Flow Meter Calibration
The mission of the Environmental Protection Agency is to protect human health and the environment. The EPA is responsible for maintaining and enforcing national environmental laws dealing with land, air, and water pollution as well as hazardous waste, endangered species, and other issues. The Ann Arbor National Vehicle and Fuel Emissions Laboratory is responsible for the complete range of tasks required to provide the necessary laboratory testing and support services to verify that Federal Emission Standards are met.
One way to test vehicle emissions outside of the lab is by collecting data using a Portable Emission Measurement System (PEMS). The flow meter attached to the PEMS unit needs to be calibrated frequently to guarantee accuracy; the EPA currently does not have an in-house method to do this. Instead, the EPA must physically send their flow meters back to the manufacturer in order to have them calibrated. This process can take up to two weeks, leaving the EPA short of flow meters, and costing them time and money. The EPA hopes to remedy this problem by developing a device that allows for in-house flow meter calibration.
Our design team constructed a fully functioning prototype based on specific operating points obtained from previous PEMS data. Testing conditions simulated exhaust temperatures and flow, and NIST traceable instruments will ensure reliability. The desired prototype is also portable. A manual detailing construction, operation, and maintenance of the prototype was included for the EPA.
ARaymond: Surface Geometry Coefficient of Friction Study
ARaymond is a global company that specializes in the design and manufacturing of fasteners and bonding agents for multiple industries. ARaymond’s products range from creating biodegradable fasteners for plants in greenhouses to industrial/commercial fasteners for photovoltaic modules.
ARaymond is currently investigating the relationship between surface geometry and the resulting coefficient of friction between two surfaces. In-depth knowledge in this correlation will lead to advancements in ergonomic design for ARaymond’s products. The team designed and built a testing system to help find these correlations with many different geometries.
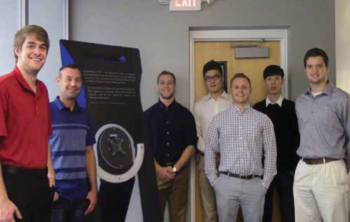
Team Members (L-R): Steven Gerdeman, Jason Reznar, Guangchao Song, David Jagow, Yewei Jiang, Sam Boyea
Whirlpool Corporation: Interchangeable Grid for Ice Cube
Whirlpool Corporation is a Fortune 500 manufacturer of household appliances, headquartered in Benton Harbor, Michigan. It produces under-counter icemakers for use in homes and small businesses. These icemakers are state-of-the-art and produce completely clear ice, free of sediment and air bubbles.
To form the ice in these icemakers, water flows onto an angled plane in very thin layers until a slab of ice is formed. From there, it is dropped onto a grid, which is comprised of heated wires. These wires melt through the slab of ice to create cubes of identical size and shape.
In order to reach a new market, a grid has been created to produce ice of different shapes that can be changed by the consumer. Some of these shapes are stars, circles, or triangles. In the future, seasonal shapes might be produced as well. Because this is a new product, the icemaker had to be retrofitted in order to be able to easily exchange the grids. Ergonomic constraints were a major factor in considering the interchangeability of the grid system in order to be able to accommodate for consumers with disabilities or physical limitations.
ArcelorMittal: Preliminary Steel Sample Rapid Cool Box
The ArcelorMittal Burns Harbor location is the second largest steel making facility in America. Products manufactured at this plant include hot and cold rolled steel, hot-dipped galvanized sheet, etc. Along with supplying the automotive market, ArcelorMittal also provides steel products for the appliance, construction, and distribution industries. The Burns Harbor location acts as an excellent highway and railroad epicenter for the 5 million tons of raw steel it produces annually.
An important standard for the company is to ensure consistency in the quality of their steel. Preliminary steel samples are formed and retrieved from one of three Basic Oxygen Furnaces (BOF) to determine the chemical composition. These samples must be cooled quickly before testing commences. The current solution calls for a metallurgical process known as quenching, where water can enter through microscopic voids in unformed samples. When these “bad” samples are tested on the Optical Emissions Spectrometer (OES), an electric arc vaporizes the water embedded in each sample. Mixed with graphite dust, water clogs the OES and can result in up to two hours of idle time.
The goal of this project was to find an effective system that would rapidly cool samples and, in turn, reduce inaccuracies/faults in the OES. Utilizing convective cooling, the updated process uses a high powered air blower to lower sample temperatures to 20 °C (room temperature) in under 30 seconds.
Fairmount Santrol – Alpha Resins LLC: Innovative Bulk Packaging
Fairmount Santrol is a leading provider of high-performance sand and sand-based products used by oil and gas exploration and production companies to enhance the productivity of their wells. The company also provides high- quality products, strong technical leadership, and applications knowledge to end users in the foundry, building products, water filtration, glass, and sports and recreation markets. Its products are delivered around the world and, as such, the products must be shipped in packaging that will protect the products from a variety of climates. Upon delivery, the products will be stored in the customer’s industrial facility without climate control for an unknown amount of time.
The project required research and development of an alternative bulk package that is able to be reused or repurposed to maintain the company’s zero landfill policy across its 30+ facilities. Additionally, the new bulk package must prevent moisture from contaminating the product, while also being heat resistant to prevent the product from fusing into a large lump, which requires rework. The new bulk package will prevent or reduce the need for product rework, while also being reusable and inexpensive.
Pratt & Miller Engineering: Formula SAE Carbon Fiber Suspension
Formula SAE (Society of Automotive Engineers) is the largest collegiate design competition in the world, which challenges students to design, manufacture, and test a small, open-wheel racecar. The Formula SAE Team has partnered with Pratt & Miller Engineering (PME). PME, founded in 1989, is an engineering firm that focuses on professional motorsports and advanced technologies. PME currently develops Corvette Racing, the most successful team in the history of the American Le Mans Series. With their advancements in motorsports, the company expanded into a full engineering firm with over 300 employees. They now serve customers in the defense, automotive, and power-sport industries.
With the support of PME, improvements to the Formula SAE vehicle were made by developing a carbon fiber suspension system. The objective was to design, manufacture, and validate a composite suspension to reduce the mass of the 2017 vehicle. This process involved performing structural analysis on the linkages while utilizing finite element analysis to design the laminate schedule of each link. Bonding strategies were researched and implemented to properly bond aluminum inserts inside the optimized carbon fiber links. The aluminum inserts house spherical bearings, which allow for proper suspension articulation. Overall, the suspension system must be able to withstand the loads generated at the tire, while being as light as possible.