Mechanical Engineering
Projects
One goal of the MSU Mechanical Engineering Program is to educate engineers who are prepared to lead, create, and innovate as their professional or graduate careers evolve. The Mechanical Engineering Design Program is the key element of the curriculum that supports this goal. There are five required design courses in the program which provide our students with eight hands-on, team-based, ‘design, test and build’ projects, and numerous opportunities to practice and refine their written, oral, poster, and video presentation skills. The Design Program in Mechanical Engineering has attracted national recognition on many occasions and helps to distinguish the ME program as one of the best in the country.
For information on becoming a project sponsor, please contact Mike Colucci.
The following are the project sponsors and projects for Fall 2015:
Kautex Textron: Improved Assembly of Fuel Tanks
Kautex Textron, located in Providence, Rhode Island, is one of the world’s 100 largest automotive suppliers. It manufactures camshafts, clear-vision, selective catalytic reduction, and fuel tank systems. Kautex has made significant advancements in fuel tank technology in recent years, revolutionizing their manufacture by constructing them from plastic materials that are lightweight, resistant to corrosion, recyclable and have many other advantages over their steel counterparts. In plastic tank systems, assembly is a two-step process in which a stud is welded or screwed into the tank and a palnut is hammered over the heat shield onto the stud. Kautex is interested in an optimized wave pad design and a method of attachment that would reduce the design lead time and the validation costs of this assembly process.
The MSU team will develop designs that reduce the need for multiple operators or machines to streamline the assembly process while meeting manufacturing constraints. An optimal design will be selected and developed in detail for implementation by Kautex Textron.
International Automotive Components (IAC): Design of a Carpet Transfer System
International Automotive Components (IAC) is an automotive supplier with 32,000 employees at 100 facilities in 22 countries and is the third largest supplier of automotive interior components in the world. Components designed and manufactured by IAC include trim systems, instrument panels, flooring systems, and overhead systems. Currently at IAC plants across North America, flooring systems are made in large quantities and are often carried by employees between each stage of the manufacturing process without assistance. These carpets can be as large as 24 square feet, may weigh up to 30 pounds and are carried over distances from one to fifty feet. This practice carries a risk of employee injury and can also cause physical strain.
IAC has asked the MSU design team to develop a carpet transfer system that will reduce the physical strain on factory employees, lower the risk of physical injury, and improve workplace efficiency. The MSU team will design and manufacture a prototype transfer system for implementation and testing at IAC facilities.
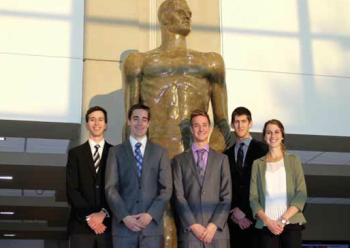
Team Members: Robert Cenowa, Kathleen Landwehr, Bradley Seegert, Joseph Senechal, Aaron Brodsky Smith
Ingersoll Rand: Redesigned Street-Elbow Assembly Process
Ingersoll Rand is a global industrial company that manufactures tools and air conditioning systems for consumers and businesses worldwide. The Climate Solutions Sector, which is a division of Ingersoll Rand, offers products which aim to help customers reduce energy and carbon emissions use while improving performance. During assembly of gas manifolds at Ingersoll Rand’s Lynn Haven plant in Florida, one of a sequence of assembly operations is problematic. A street elbow is attached to the manifold using a torque gun, which frequently results in the street elbow being orientated incorrectly. The operator must then use a wrench to reposition it.
MSU students were asked to reduce or eliminate the need for the repositioning procedure, thus reducing or eliminating the street elbow’s ergonomic score. Ingersoll Rand wants to make the manifold assembly as safe and streamlined as possible to prevent long-term injuries to personnel. The team will design a new assembly process that fulfills Ingersoll Rand’s specifications. It will begin with tests of existing torque guns and ultimately result in the demonstration of new methods of assembly to improve the ergonomic score.
Ingersoll Rand: Removal System for a Fan Motor
Ingersoll Rand is a multinational engineering company with divisions that specialize in transportation, manufacturing, construction and agriculture. One division, Trane, specializes in heating and cooling air control. Trane manufacturers large air handling units (AHU’s) for its semi- customized commercial market. These units house multiple stacked fans that can weigh up to 500 lbs. Since these fans run constantly, their maintenance is important. Their motors are heavy and removing them for maintenance or replacement can be difficult and dangerous. Trane will be launching a new AHU model and wishes to develop a reliable and consistent method of removing the AHU’s fan motors safely.
The team at MSU will design and develop a safe, reliable motor-removal solution using a rail system for removal and lifting of the motors to a doorway, through which workers can handle them safely. The team will construct a prototype of the optimal design for evaluation by Trane.
Tenneco Inc.: Improved Catalytic Converter Assembly Process
Tenneco Inc. is a leading manufacturer of automotive exhaust systems and catalytic converters, which have been used for emission control in vehicles since 1975. In its Grass Lake, Michigan, engineering facility, Tenneco designs converters which are manufactured at plants throughout the United States. The chemically-active component of a catalytic converter is a ceramic substrate that is wash- coated in precious metals, which undergo catalytic reaction with certain species of the exhaust gas to clean the emissions of the vehicle. The substrate is wrapped in a mat, typically made of ceramic fibers, to hold it in place within the can. While the contents of the catalytic converter are generally dictated by requirements of the customer, the process by which the contents are ‘canned’ is inefficient and inconsistent and offers significant opportunities for improvement.
The goal of this project is to design an improved manufacturing technique for ‘canning’ the substrate and mat, which may be optimized by altering the geometry or changing the mat material. The resulting catalytic converter should be constructible with greater manufacturing consistency while meeting or exceeding the quality and performance of current designs.
Meritor: Lightweight Trailer-Axle Hub
Headquartered in Troy, Michigan, Meritor is a leading global supplier of innovative products for commercial-vehicle and industrial markets. These products include axles, brake and safety systems, drivelines, suspensions, trailer components, and aftermarket parts. Meritor produces more than 50 different trailer axles for a broad range of trailer applications, all of which require a hub component as part of the wheel-end assembly. The current trailer- axle hub sold by Meritor is made of ductile iron and competes with lower quality but lighter hubs produced by other companies. Lightweight hubs are desirable to customers because less weight corresponds to lower rotational inertia. Meritor is interested in designing a new, lightweight design trailer-axle hub that meets the performance quality of Meritor’s existing iron products.
The MSU design team will create an optimized design of Meritor’s trailer-axle hub so that the company can introduce a more competitive product into the hub market that still meets the desired strength and durability requirements. The team will benchmark hubs from Meritor and its competitors, determine ways in which weight can be reduced and select an optimal design using optimization software.
Marathon: Hazardous-Vapor Isolation Plug for Pipelines
As the nation’s fourth-largest oil and natural- gas refiner, Marathon Petroleum Corporation operates over 8,300 miles of pipeline for transporting fuels and marketing petroleum products. Based in Findlay, Ohio, Marathon Petroleum owns a variety of storage facilities throughout the Midwest. One of these facilities, located in Woodhaven, Michigan, has seven storage reserves at which butane is stocked in caverns roughly 1,500 feet below the earth’s surface. Butane is pumped between tank trucks and these caverns through thousands of feet of pipeline which require continuous maintenance. One of Marathon’s maintenance projects requires the refurbishing of the well heads to the storage caverns. Marathon strives to protect workers against hazardous vapors that may escape during such operations, since safety is a top priority. Therefore, Marathon is interested in installing an isolation plug which, when placed between the production and service casings, can block all potentially hazardous or explosive gas emissions.
The Capstone team will design and model an annular, isolation plug for Marathon’s pipelines. The plug must meet Marathon’s functionality, reliability, and durability requirements. A final, working prototype will be delivered to the company prior to the course deadline and tested for performance at the site.
Michigan AgrAbility: Redesign of a Skid-Steer Vehicle for Ease of Access
Easter Seals Michigan AgrAbility is a nonprofit organization that provides assistance to farmers with handicaps, injuries, or conditions due to aging. Services include creative solutions through the development of tools, equipment, and methods to improve each farmer’s daily quality of life. A skid-steer, which is a vehicle designed for a variety of tasks in farming and construction, is the one such device that AgrAbility has modified to accommodate its clients’ needs. Due to its versatility, a skid-steer is an essential tool for a farmer’s day-to-day tasks. However, getting into skid-steers with a front-loading driver’s seat requires dexterity and flexibility which many farmers with disabilities lack. Therefore, Michigan AgrAbility is interested in creative modifications that could be made to the skid-steer to help disabled farmers get into and out of their personal vehicle.
The major factors that constrain design solutions are the dimensional limitations presented by the motion of the skid- steer arm assembly and the inability to alter the vehicle’s roll cage under the terms of its warranty. This team’s challenge is to design, build, and test a mechanism that would allow the disabled client to get into and out of the skid-steer safely and efficiently. A prototype will be constructed and delivered for testing.
*This is a joint project of the MSU Cooperative Extension and Michigan Easter Seals, funded by the US Department of Agriculture.
ArcelorMittal: Exhaust Gas Sensor for an Annealing Furnace
ArcelorMittal is the world’s leader in steel production and mining. In order to remain competitive in many steel markets, the company must operate multiple finishing-product lines. In such lines, one widely-used method of steel processing is annealing. During this process, steel coils are loaded into ovens heated by furnaces for a prescribed amount of time in order to remove stresses introduced during manufacturing processes. The furnaces vent some exhaust fumes into the processing facility, which can create a hostile work environment for employees, especially if combustion in the furnace is not ideal. While combustion gas analyzers are available for measuring furnace exhaust properties and as personal meters for individuals, the constraints on their operation require a carefully designed gas-sampling strategy to ensure workplace safety.
In order to minimize downtime and eliminate the need for expensive combustion analyzers, the Michigan State team will develop a method of collecting and cooling furnace exhaust gases. The gas cooling will be substantial enough to meet the sample temperature requirements of individual employee gas meters. The team will present a prototype design, justification and analysis to ArcelorMittal for future implementation.
Robert Bosch: Waste Heat RecoverySystem for Vehicles
Robert Bosch is a pioneer in research, development and production of automotive, consumer and industrial components and systems for manufacturers worldwide. With the ongoing efforts to improve Diesel engine efficiency and environment sustainability, Bosch has developed a Waste Heat Recovery system (WHR) for heavy-duty commercial vehicles. WHR utilizes approximately 60% of invested primary energy through an Organic Rankine Cycle (ORC) in which ethanol is circulated; it converts exhaust waste heat into useful energy for powering mechanical or electrical systems in a vehicle. This system guarantees fuel savings of up to 5% and a reduced output of CO2, which will help to meet future emission limits. Currently Bosch uses a tank as one component of the ORC, which maintains ethanol at a constant pressure and volume. Determining the amount of ethanol required for the ORC is necessary for it to recover waste heat at maximum efficiency. The tank also needs to be designed with long-lasting components and materials to overcome durability and leakage problems.
The team will design and fabricate a tank which maintains the optimal amount of ethanol at constant pressure and volume for maximum efficiency. It will also specify components and materials needed for a durable, leak-free design. Structural design calculations and finite element analyses will be used to ensure the design meets the requirements of minimum weight and fabrication cost.
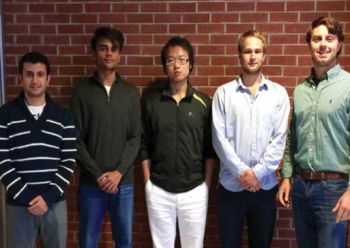
Team Members: Abdulmajeed Alotaibi, Alexander Theodore Bibicoff, Ryan De Tour, Ankit Sharma, Zhengyuan Xie
Environmental Protection Agency: Efficient Heating of a Dilution Tunnel
The Environmental Protection Agency (EPA) is a government organization that regulates and enforces laws that pertain to the cleanliness of the environment. One of the main concerns of the EPA is vehicle emissions. The EPA tests all car models sold in the U.S. to ensure they meet exhaust-gas emission standards. A common method of measuring emissions is to remove the engine from a vehicle and run it under controlled conditions on a dynamometer, collecting exhaust gas for emissions analysis. In order to accurately measure the concentrations of emissions in the exhaust, the sampled gas must be cooled prior to analysis to stop chemical reactions that would continue in uncooled high-temperature gas. The desired cooling is achieved by introducing a controlled flow of air at a specific temperature upstream from the engine exhaust, and mixing it with the exhaust gas in a dilution tunnel.
This team’s objective is to design a system to heat the incoming dilution tunnel air to 47 °C +/- 5 °C as efficiently as possible. To accomplish this, the team proposes a design that utilizes as much waste heat from the engine as possible in order to minimize the requirement for additional electrical heating to reach the desired temperature. The proposed system will be tested on the EPA’s dilution tunnel.
Hitachi Automotive Systems America, Inc.: Test Bench for Direction-Injection Fuel Systems
Hitachi Automotive Systems is involved in the development, manufacture, and sale of automotive components and systems, and its Farmington Hills location is home to the fuel system team. A principal objective in automotive design is to maximize the fuel efficiency of vehicles in every way possible in order to meet environmental impact regulations. One method by which fuel efficiency can be increased is through the use of gasoline direct-injection fuel systems in preference to traditional port-injected systems, as they permit more precise control over the amount of fuel injected, which can reduce fuel consumption. Another method of improving fuel efficiency is by using blends of fossil and alternative fuels in optimal ratios.
The goal of this project is to design a testing bench for a gasoline direct-injection fuel system comprising six injectors. A successful design will allow the fuel system team to perform experiments that monitor the performance of an injection system using different fuel blends and to measure the fuel flow through each injector. With such tests, Hitachi may ultimately design the most efficient fuel systems for the automotive market of the future.
Tenneco Inc.: Design of a Passive Exhaust Valve
Tenneco Incorporated is one of the world’s leading designers, manufacturers, and distributors of clear-air and rid-performance product systems within the automotive industry. In many of the muffler systems that Tenneco designs, high pressure gas passes through a passive exhaust valve before freely entering the atmosphere. Recently, it has been observed that, if designed properly, a back-pressure can be induced in the passive exhaust valve, which can in turn, prevent approximately 2-3% of NOx emissions from reaching the atmosphere, effectively aiding in the reduction of greenhouse gas emissions. Tenneco is interested in design concepts that improve upon the functionality of the back-pressure-induced exhaust valve, which also meet decibel, temperature, lifespan, and cost regulations of the product.
The MSU team will evaluate a set of conceptual part-minimizing designs that satisfy the constraints set by Tenneco. An optimal design will be selected and then customized for a particular Tenneco muffler. A prototype of the most promising design will then be built and tested for functionality and reliability and delivered to Tenneco for further evaluation.
Whirlpool: Design of an Appliance Pedestal Attachment
Whirlpool Corporation is the world’s largest manufacturer of appliances. It produces models for several of the most popular brands in over 70 manufacturing facilities around the globe. One of its products is a pedestal attachment for washers and dryers that raises the appliance and provides a drawer for storage. During installation, the appliance must be laid on its back so that the pedestal can be fastened to it with screws. However, many laundry rooms are not large enough for this attachment process, in which potential customers may consider other brands. Furthermore, the appliances are not designed to be laid on their backs as they contain concrete counterweights. Whirlpool is, therefore, interested in pedestal attachments that maintain the structural and vibrational characteristics of the current design but do not require an installation process in which the appliance is laid on its back.
The MSU team will conceive and evaluate multiple designs that satisfy Whirlpool’s constraints. An optimal design will be selected and a prototype will then be built and tested for preliminary functionality and reliability. This design will be delivered to Whirlpool for further evaluation and optimization.
Trickl-eex/MSU Department of Entomology: Advanced Orchard Spraying System
The MSU Organic Pest Management Lab is a research lab based in the Entomology Department. It conducts research on a variety of Michigan and Great Lakes agricultural commodities. The goal of its research is to provide economically viable pest management strategies for organic farming. The lab is currently developing an optimized Solid Set Canopy Delivery System (SSCDS) for multiple applications by tree fruit producers. This delivery system is a network of lines and sprayers installed throughout an orchard that is used in place of traditional air-blast tractor-based spraying techniques. The long-term goal of the SSCDS project is to better manage expensive chemical products, improve pest and crop management and reduce labor costs. This enables tree fruit producers to remain globally competitive and environmentally responsible.
The engineering focus of this project is to optimize the existing SSCDS by reducing the waste of expensive pest management products. Our optimized design will utilize fluid analysis to create a more efficient reservoir delivery system with scalability to multi-acre orchards. A working pressure-driven prototype will be designed and built to demonstrate how the system reduces waste and decreases operating costs.
Michigan Seamless Tube: Evaluation of Eddy Current Heating of Pipelines
Since its formation in 1927, Michigan Seamless Tube has manufactured high-chrome mechanical and pressure tubing and piping for numerous industries. Michigan Seamless Tube continues to develop its cold-drawn pipe- manufacturing technology, which allows pipes to be manufactured to customers’ precise specifications. Michigan Seamless Tube recently developed a tube for the oil transportation industry, manufactured using a cold-drawn technique, to serve as a heating tube for an end manufacturer’s pipeline. The tubes are heated internally by electrical eddy currents imparted around their periphery, which then heats the outermost layer of oil making it less viscous. Thus skin-heating of the tube facilitates oil flow.
The objective of this project is to evaluate and compare the performance of cold-drawn tubes with hot-finished tubes, and tubes made with other manufacturing processes. An apparatus will be designed to measure the uniformity and efficiency of conduction eddy currents in each kind of tube, and to examine the effect of wall uniformity on performance. The efficiency with which oil can be heated by eddy currents is a significant economic factor in pipeline- tubing selection since oil pipelines are often over 35 miles long and are expected to last several decades.
Heartwood School: Therapeutic Mechanical Pony
The children at Heartwood School in Mason, Michigan, have non-typical physical conditions associated with movement and balance. From an early age, they struggle with everyday tasks such as sitting or balancing. In order to develop the coordination and strength necessary for these skills, core muscles need to be engaged and strengthened through therapy and exercise in a durable, safe device. The faculty at Heartwood currently has few devices for this process and each has limitations. The absence of either essential support or specific muscle targeting reduces the therapist’s ability to improve the child’s functionality. Furthermore, existing devices do not inspire the child to participate proactively in exercises.
The MSU team will develop a therapeutic mechanical pony that will help students with physical disabilities exercise and improve their core muscle strength. Through the use of a wobble seat and adjustable components, the therapist will be able to properly engage with the student during sessions and adapt the exercise to each student’s skill set. The pony will also have cosmetic features to captivate the student’s imagination and reinforcing components to inspire improvement.
Hitachi Automotive Systems Americas, Inc.: Redesign of a Variable Timing Camshaft
Hitachi Automotive Systems manufactures and markets a broad range of electro- mechanical and electronic products for all major automotive original equipment manufacturers. The focus of this project is the Hitachi Variable Timing Camshaft (VTC). The VTC is attached to the end of the camshaft and uses rotational force driven by oil pressure to vary the valve-event timing. This assembly requires locking pins to prevent movement between the body, vane, and its other components. The positioning of these pins during assembly must satisfy tight tolerances to hold the components correctly and achieve the required initial backlash during engine start-up. However, the Hitachi’s suppliers lack the ability to meet this tight tolerance specification, resulting in a high scrap rate.
The goal of this project is to investigate new assembly methods that can achieve precise component location and sufficient initial backlash without such a tight dependence on tolerances. A relaxation of component tolerances will lower the scrap rate at assembly. By reducing these operational costs, Hitachi will remain a competitive supplier to automotive companies.
Ford Motor Company: Dynamic Friction Rig for Driveline Joints
Ford Motor Company is one of the largest automakers in the world with its headquarters located in Dearborn, Michigan. Ford conducts rigorous testing and modeling of all its parts to ensure the high quality of every automobile produced. However, it is currently unsatisfied with its driveline Computer-Aided Engineering (CAE) models. Ford lacks sufficient information on driveshaft. It is particularly difficult to characterize dynamic friction in driveline joints while under torque. Ford has attempted to develop a test rig for acquiring the data needed to improve understanding of dynamic friction behavior, but the range of speeds and torques of the current fixture is inadequate. Improving this aspect of data measurement and model development would help Ford enhance its ability to predict and resolve noise, vibration, and harshness problems prior to construction of prototypes, which would significantly save cost and design time.
Ford has requested that the MSU team design and construct a test rig that will be used to measure driveshaft. The rig will measure articulation torque vs. angle in real time over a significantly larger range of driveshaft torques and speeds than the current rig. These results will then be used to improve current Ford computer-aided engineering models.
Ford Motor Company: Automated Assembly of Vehicle Fascia
Ford Motor Company is a world-renowned automotive company headquartered in Dearborn, MI. Ford has partnered with Dakkota Integrated Systems in Chicago, IL, to develop an efficient and flexible robotic cell to quickly attach rear park aid sensors to front vehicle fascias. Designed by JR Automation, this robotic cell will load the fascia onto a fixture, punch holes in its side, glue the sensor into the holes, unload the fascia to a loading nest, and then repeat the process for the next fascia in the production sequencing. This design group’s task is to assess and improve this robotic process.
The MSU team will evaluate the consistency and accuracy with which the robot locates and punches each hole in the fascia. When a hole-punching process of sufficient accuracy and repeatability has been devised and implemented, the robotic cell will be tested at full capacity and then deployed by Dakkota Integrated Systems.
Fiat Chrysler Automobiles: Design and Simulation of Automatic Transmission System for Washing Machines
Fiat Chrysler Automobiles (FCA), located in Auburn Hills, MI, is a multinational manufacturer of automobiles and is currently the world’s seventh largest. The transmissions used in many of its cars and light trucks have 250,000-mile warranties and, if the transmission fails before this mileage is reached, the company must compensate the customer. It is, therefore, useful to analyze data that portray the driving cycles and loads imposed on transmissions by the average driver in different regions of the world. These data assist engineers at FCA in designing automatic transmissions for their vehicles that perform optimally when driven in a variety of different ways. FCA’s design target is for each transmission to have an average durability that exceeds 150,000 miles.
By modeling a transmission using a simulation program that incorporates a particular driving cycle, fatigue and stress analyses can be carried out at selected locations within a transmission to determine whether the 150,000-mile durability target is feasible with a given design. In cases when this design target is predicted to be unfeasible, suggestions will be made for design optimizations that would produce the most durable transmission.